Может, махнём куда-нибудь вечером, – слышен голос моего друга (пилота, КВС А320) в телефонной трубке. – Сегодня не могу, улетаю в командировку, – отвечаю я. – Куда? – В Верхнюю Салду. – А это где? – Как, ты не знаешь? Это же титановая столица мира, – говорю я с укоризной в голосе, а сам думаю: действительно, а где это?
Из столицы России до столицы Урала г. Екатеринбург всего 2,5 часа лётного времени, а далее – 180 км. на машине минуя Нижний Тагил в Верхнюю Салду. Всего пять с половиной часов, и мы у цели. В этом городке с населением около 50 000 человек расположена Корпорация ВСМПО-АВИСМА – крупнейший в мире производитель титановой продукции.
Информация о деятельности корпорации проходит через нашу редакцию достаточно часто, но, учитывая некоторую закрытость предприятия, чувствую пробелы в знаниях. Поэтому гостеприимные хозяева в первую очередь ведут нас в заводской музей. А пока вы будете знакомиться с фотографиями экспонатов музея, я расскажу немного истории.
В 1927 году правительство СССР принимает решение о строительстве Кольчугалюминиевого (дюралевого) завода мощностью 1200 тонн. И уже 1 июля 33 года в Москве заработал Завод № 95, который стал основным поставщиком полуфабрикатов из алюминия и его сплавов для советского самолётостроения. В 1941 году завод эвакуируется на Урал. Так Верхняя Салда, которая только в 1938 году получила статус города, превратилась в один из крупнейших промышленных центров Советского Союза.
Во второй половине 50-х на предприятии началось освоение технологий проката титановых листов. В феврале 1957 г. на ВСМПО был выплавлен первый титановый слиток весом 4 кг., что стало отправной точкой в промышленном освоении производства российского титана. И мои слова про «титановую столицу мира» – никакое не преувеличение. В 80-е годы прошлого столетия Салда производила титана в полтора раза больше чем весь остальной мир.
В 90-е начинается реализация стратегии интеграции ВСМПО в мировую экономику. В 1998 г. ВСМПО и АВИСМА образуют группу компаний, связанных единой технологической цепочкой – от сырья до конечного продукта. АВИСМА - ещё одно предприятие города, на котором (тогда БМТК), в 1960 г. был впервые получен губчатый титан (исходное сырьё, производимое из ильменита). В 2005 г. образовано единое юридическое лицо ОАО «Корпорация ВСМПО-АВИСМА».
Так, в результате этих преобразований корпорация (предприятия которой когда-то были ориентированы исключительно на внутреннее потребление) стала основным стратегическим поставщиком изделий из титана более 300 фирм из 48 стран мира, в том числе – ведущих мировых авиастроителей. Одни имена чего стоят: Bombardier, Rolls Royce, Airbus, Snecma, Honeywell, Boeing, General Electric, Embraer, Pratt&Whitney и многие другие известные фирмы. Конечно же, потребителями продукции корпорации являются и все российские компании, работающие на авиацию и космос.
Вот так «по-варварски» можно вкратце изложить 87-летнюю историю предприятия и его достижения, о которых нам рассказывали около полутора часов. Но иначе и быть не может. История и статистика – это удел учёных-историков и экономистов-стратегов. Наш же интересует технологический процесс. Поэтому, отказавшись от обеденного перерыва, спешим в Плавильный цех (№32).
И первый участок – Прессовый. Здесь расположены вертикальные гидравлические прессы (усилием 25, 50, 100 МН) для прессования электродов, формируемых из губчатого титана, возвратных титановых отходов, лигатур и чистых металлов (Al, Cr, Zn, Si, Mn, и др.) В результате получают прочный крупногабаритный электрод, вес которого равен весу выплавляемого слитка.
На первый взгляд может показаться, что электрод состоит из каких-то металлических обрезков и мусора. На самом деле, здесь работают участки рентгеноконтроля материалов, включаемых в сплав. Ничего случайного не должно попасть в электрод. Например, у всех, пересекающих границу цеха, изымают шариковые ручки, так как даже шарик стержня, изготовленный из вольфрамового сплава, попав в титановый слиток, может нанести непоправимый ущерб прочности будущего изделия.
Плавка электродов происходит в вакуумно-дуговых печах (одна плавка длится 18 часов), таких здесь 50. В корпорации имеются и уникальные подовые гарнисажные печи с дуговым источником и плазменно-дуговая печь, которая позволяет получать суперчистые сплавы для деталей роторного качества (лопатки, диски). Первичная плавка электрода в вакуумно-дуговой печи происходит со скоростью 18-20 кг. в минуту. Полученный слиток подвергается механической обработке, после чего приобретает «товарный вид». Для получения авиационного титана его переплавляют 2-й раз (скорость плавки 32-34 кг./мин.), а для роторного и в третий.
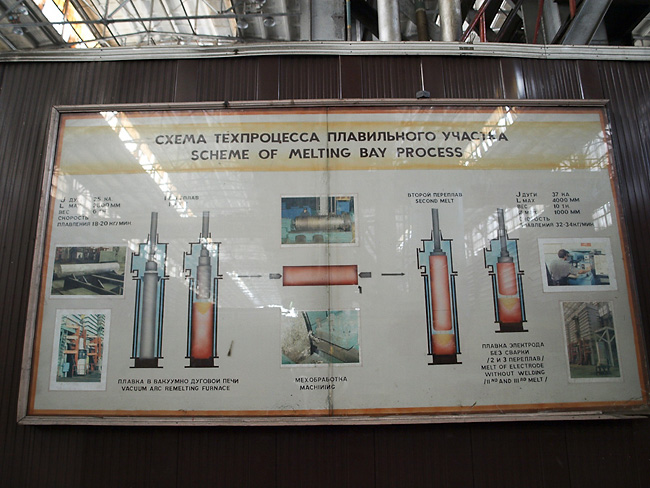
Для производства плоского проката в Корпорации имеются станы горячей и холодной прокатки. Но нас, в первую очередь, интересует продукция для авиационных потребителей, поэтому, следующий в нашей программе - Кузнечно-прутковый цех (№22). Здесь производят титановые биллеты диаметром 130-350 мм. Для ковки биллетов используются гидравлические прессы, радиально-ковочную машину и ковочные молоты. Говорят: «на огонь, воду и чужую работу можно смотреть бесконечно». Так вот, за работой (а скорее танцем) гидравлического пресса действительно можно смотреть бесконечно. Это и огонь, и работа, и вода в виде капель вашего пота, стекающего по разгорячённому лицу.
Кольцераскатной стан позволяет получать кольца наружным диаметром до 2400мм, высотой до 600 мм и массой до 1,5 тонн. И ковка биллетов, и раскатка колец происходят в полностью автоматическом режиме.
А вот мы приблизились и к наиболее интересной для нас части производства. На предприятии производятся поковки штампованные различной конфигурации и назначения, и, в первую очередь, для авиационной промышленности: конструкционные (фюзеляжные, шассийные) и роторные (диски, лопатки, валы). При проектировании технологии производства штамповок применяется математическое моделирование технологического процесса (с использование программы DEFORM). В 22-м цехе расположена зона конечного контроля и упаковки продукции.
Конечно же, самое потрясающее зрелище - Кузнечный комплекс. Цех №21 - здесь расположен самый мощный в мире гидравлический пресс усилием 750МН (высота 22 метра, глубина фундамента 20 метров, построен в 1961 году), а также прессы усилием 200 МН и 300 МН, гидравлический пресс изотермического прессования – 40 МН, гидровинтовые прессы – 56 МН и 63 МН, и штамповочные молоты с массой падающей части 4, 6, 13, 23 т. Даже страшно представить, какая гигантская мощь заключена в этих механизмах.
Цех механической обработка штамповок (№54).Экскурсию по этому цеху генеральный директор ОАО "Корпорация "ВСМПО-АВИСМА" Михаил Воеводин проводит сам. Здесь происходит черновая механообработка штамповок на современном высокотехнологичном оборудовании. Здесь же расположено оборудование для ультразвукового контроля продукции и координатно-измерительная лаборатория. Заходим в цех, останавливаемся и засыпаем гендиректора вопросами.
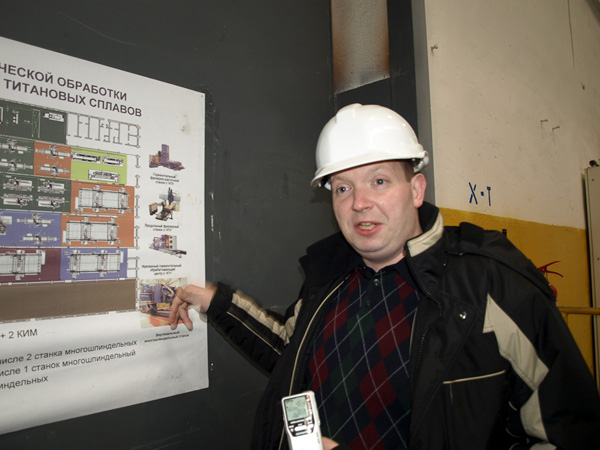
генеральный директор ОАО "Корпорация "ВСМПО-АВИСМА" Михаил Воеводин
- Михаил Викторович, масштабы предприятия, продукция, список партнёров просто поражают. Неужели вы вне конкуренции на мировом рынке?
- Напротив, конкуренция только усиливается. Да, у нас есть серьёзные конкурентные преимущества, но это только сегодня, а завтра… Крупные авиапроизводители стремятся сократить число поставщиков. Им выгодно получить продукт в как можно более высокой степени готовности. Если раньше у нас брали штамповку и везли её на другое предприятие для механообработки, то теперь мы инвестируем значительные средства в развитие собственного потенциала по механообработке (ред: инвестиции в модернизацию производства – 650 млн. долларов США за 3 года). Заказчик заключает один контракт с ВСМПО, сразу с механообработкой деталей. Это уникальная услуга и никто в мире этого пока не делает.
- Механообработка это высокодоходный бизнес?
- Нет. Сама черновая механообработка большой добавочной стоимости не имеет.
-Тогда есть ли смысл в таких инвестициях и где ж прибыль?
- В стружке, - говорит Михаил Воеводин, хитро улыбаясь. – Да вы скоро сами всё увидите.
Изучая технологический процесс, постепенно постигаю азы «титановой экономики»: штамповка заготовки для тележки шасси Airbus A380 весит 3,1 тонны, а после механообработки – 1т. 800 кг. Раньше заказчик получал эту заготовку, платил за транспортировку каждого килограмма веса на другое предприятие, где и производилась её черновая механообработка. Вот и получается, что механообработка на месте позволит ему получить значительную экономию на логистике, а более тонны высококачественного титана (в виде стружки), который раньше доставался «посреднику» бесплатно, останется в Салде и пойдёт в переработку.
В этот момент «титановый пазл» начинает складываться в голове. Вот он - ключик к разгадке повышенного интереса Боинга к Верхней Салде. Самолёт Boeing 787 Dreamliner на 15% сотоит из титана. Теперь понятно, почему Boeing пошёл дальше других партнёров и совместно с ВСМПО-АВИСМА на территории предприятия создал СП ЗАО «Ural Boeing Manufacturing» (доли: 50/50). Совместное предприятие с Боингом в России – ещё недавно даже мысли об этом были из области фантастики. А сегодня с производством UBM нас знакомит руководитель СП Гарри Бейкер
Предприятие по черновой механической обработке титановых штамповок для Boeing 787 Dreamliner было открыто 7 июля 2009 года. Здесь установлены современные пятишпиндельные пятиосевые копировально-фрезерные станки с ЧПУ. Появление СП позволило создать замкнутый производственный цикл. Например, штамповка нижней хорды фюзеляжа Boeing 787 весит 1200 кг. После механообработки её вес снижается втрое (прим: вес готовой хорды при установке на самолёт уже всего около 250 кг.). А вся титановая стружка возвращается на ВСМПО-АВИСМА и используется вторично.
Что ж, отраден факт, что Россия со своими технологиями пытается встроиться в глобальную мировую экономику. И в некоторых областях это удаётся вполне успешно. Хочется верить, что это не будет приятным исключением, а наши потомки действительно будут гордиться тем, что отечественные конструктора, инженеры, рабочие принимали участие в таком глобальном мировом проекте как Boeing 787 Dreamliner
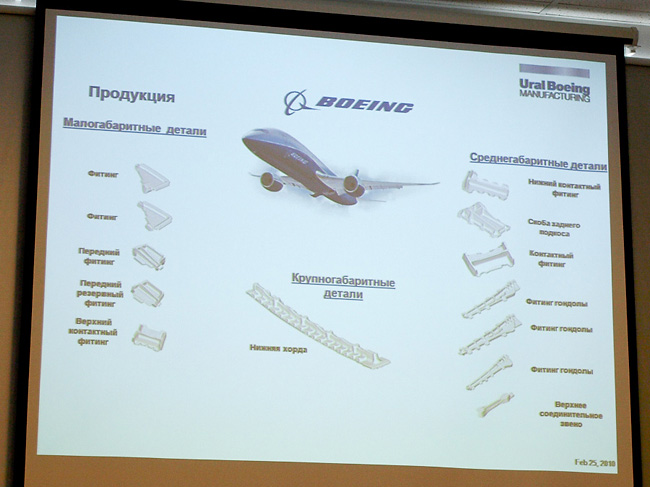
фото автора